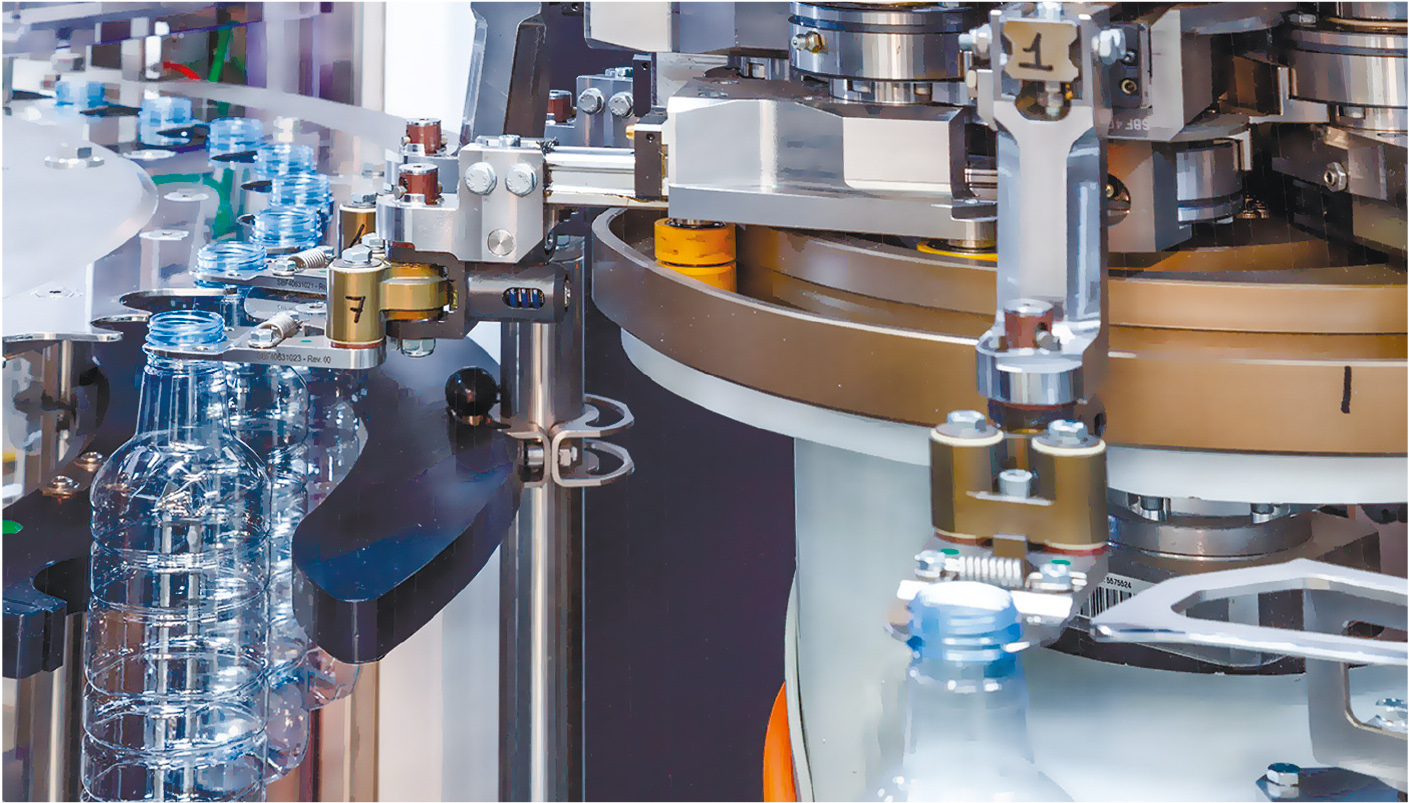
Монтаж автоматизации на производственных линиях является важным этапом модернизации и повышения эффективности работы предприятий. Автоматизация процессов позволяет значительно снизить трудозатраты, повысить точность и качество продукции, а также улучшить безопасность. Внедрение автоматических систем управления и контроля в производственные процессы обеспечивает непрерывность работы, минимизирует человеческий фактор и способствует оптимизации производственных мощностей.
Внедрение систем управления
Внедрение систем управления на производственных линиях — это ключевой элемент для повышения производительности и обеспечения оптимального контроля за технологическими процессами. Современные системы управления могут включать в себя как программируемые логические контроллеры (PLC), так и более сложные распределенные системы управления (DCS). Эти устройства помогают отслеживать и регулировать различные параметры процесса, такие как температура, давление, скорость и другие критические показатели.
Одной из главных задач внедрения системы управления является повышение точности работы оборудования. Благодаря автоматическому контролю можно избежать ошибок, связанных с человеческим фактором, что особенно важно на сложных и высокотехнологичных производственных линиях. Программируемые контроллеры могут интегрироваться с различными датчиками, обеспечивая оперативное реагирование на изменения в процессе. Кроме того, системы управления могут быть связаны с централизованными базами данных, что позволяет отслеживать работу всего производства в режиме реального времени и на основе этих данных оптимизировать процессы.
Внедрение таких систем также способствует снижению затрат на обслуживание. Автоматические системы могут диагностировать неисправности и предупреждать об угрозах, что позволяет оперативно реагировать на поломки и минимизировать время простоя оборудования. Важно, чтобы система управления была адаптирована под конкретные потребности производства и могла работать в условиях, характерных для данного предприятия. Это требует тщательного проектирования и настройки всех элементов системы, включая оборудование, программное обеспечение и интерфейсы для взаимодействия с операторами.
Наконец, системы управления помогают повышать безопасность на производственных линиях. Использование автоматических контроллеров позволяет исключить опасные ситуации, связанные с перегрузкой оборудования или нарушением технологического процесса. В случае аварийной ситуации система автоматически приостанавливает или корректирует работу линии, предотвращая серьезные последствия.
Подключение датчиков и контроллеров
Подключение датчиков и контроллеров является неотъемлемой частью автоматизации производственных процессов. Датчики, устанавливаемые на различных участках линии, позволяют собирать данные о параметрах, таких как температура, давление, влажность, скорость и уровень жидкости. Эти данные поступают в контроллеры, которые, в свою очередь, анализируют информацию и принимают решения о регулировке процессов. Правильная интеграция датчиков и контроллеров позволяет обеспечить точное и бесперебойное функционирование системы.
Процесс подключения начинается с выбора подходящих типов датчиков, которые соответствуют специфике производства. Это могут быть термодатчики, датчики давления, расходомеры и другие устройства, предназначенные для измерения критических показателей. Важно, чтобы датчики были устойчивыми к воздействиям окружающей среды и обладали высокой точностью. После установки датчиков они подключаются к программируемым логическим контроллерам (PLC) или другим управляющим системам, которые обрабатывают полученные данные.
Датчики должны быть правильно настроены, чтобы минимизировать погрешности и обеспечить точную передачу информации. Контроллеры, в свою очередь, на основе полученных данных могут выполнять необходимые операции, такие как регулировка параметров или запуск/остановка оборудования. Чтобы обеспечить эффективное подключение, необходимо учитывать не только технические характеристики датчиков, но и совместимость с другими компонентами системы автоматизации. Все соединения должны быть надежными и защищенными от возможных помех.
Неправильно настроенные или плохо подключенные датчики могут привести к сбоям в работе системы и даже повреждению оборудования. Поэтому после подключения датчиков и контроллеров обязательно проводится тестирование всей системы. Это включает проверку правильности работы всех компонентов, а также диагностику на возможные ошибки в передаче данных. Важно, чтобы специалисты регулярно проводили обслуживание и калибровку датчиков, чтобы поддерживать их в исправном состоянии и гарантировать надежную работу автоматизированной системы.
Программирование и настройка
Программирование и настройка системы автоматизации играют ключевую роль в обеспечении эффективной работы производственных линий. Программируемые логические контроллеры (PLC) и другие управляющие устройства требуют тщательной настройки, чтобы система могла корректно обрабатывать данные с датчиков и выполнять необходимые операции. Процесс программирования включает в себя создание алгоритмов, которые будут определять действия системы в зависимости от входных данных, поступающих с датчиков, и команд, поступающих от оператора.
Важным этапом является разработка программы управления, которая позволяет автоматизировать весь производственный процесс. В процессе программирования учитываются параметры, такие как скорость работы оборудования, режимы работы, условия для срабатывания аварийных остановок и другие важные факторы. Каждый контроллер и датчик программируются таким образом, чтобы они взаимодействовали с другими элементами системы и передавали информацию в реальном времени для обработки и анализа.
Кроме того, необходима настройка параметров системы управления. Это включает в себя настройку пороговых значений для каждого датчика, чтобы система могла своевременно реагировать на изменения условий. Настройка программного обеспечения также включает в себя установку интервалов для опроса датчиков, алгоритмов обработки данных и определения условий для активации исполнительных механизмов. Все эти параметры должны быть точными и соответствовать требованиям производственного процесса.
После завершения программирования и настройки системы проводится тестирование. На этом этапе проверяется правильность работы всех алгоритмов, а также функционирование системы в реальных условиях. Тестирование позволяет выявить возможные ошибки в программном обеспечении или неправильные настройки, которые могут привести к сбоям в работе оборудования. Только после успешного тестирования и отладки система может быть введена в эксплуатацию, обеспечивая бесперебойную работу производственной линии.
Обслуживание и тестирование автоматических систем
Обслуживание и тестирование автоматических систем — это важный процесс, который обеспечивает их бесперебойную работу и долгосрочную эксплуатацию. Даже самая современная автоматизация требует регулярного контроля, так как износ элементов системы, внешние воздействия и обновления программного обеспечения могут повлиять на ее эффективность. Основная цель обслуживания — предотвратить сбои в работе оборудования и своевременно выявить потенциальные проблемы, которые могут привести к нештатным ситуациям.
Во время регулярного обслуживания специалисты проводят проверку всех компонентов системы: контроллеров, датчиков, исполнительных механизмов и соединений. Это позволяет оперативно обнаружить и устранить возможные неисправности. Например, важно следить за состоянием проводки, проверять герметичность соединений и состояние кабелей. Кроме того, ключевым моментом является калибровка датчиков, чтобы они продолжали обеспечивать точность измерений. Периодические проверки системы охлаждения и электрических соединений также играют важную роль в предотвращении перегрева и сбоев.
Тестирование автоматических систем предполагает не только выявление ошибок в текущей конфигурации, но и проверку работы системы в условиях, максимально приближенных к реальным. Это включает в себя проведение нагрузочных тестов, когда система работает на предельных значениях нагрузки для оценки ее стабильности и надежности. Важно, чтобы все рабочие процессы могли протекать без перебоев, даже при внезапных изменениях в производственных условиях.
Кроме того, проведение интервальных проверок программного обеспечения позволяет своевременно обновлять алгоритмы управления и повышать общую эффективность работы автоматизации. В случае возникновения новых требований или изменений в производственных процессах, программное обеспечение системы должно быть адаптировано для их учета. Регулярное обслуживание и тестирование гарантируют, что автоматические системы будут продолжать работать на высоком уровне, снижая вероятность аварий и увеличивая производственные мощности.